Lessons Learned from Testing Exoskeletons
Airbus
GERMANY
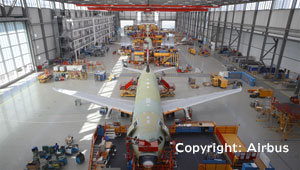
This presentation gives an overview on the special needs for exoskeletons applicable in the aerospace industry. Further, the study shows an example of the development and testing history of one selected exoskeleton. The presentation concludes with a discussion on the potential and challenges of future exoskeletons.
Human-centred Workplaces. Modelling and Simulation of Advanced Factory Environments Integrating Intelligent and Adaptive Exoskeletons
Fraunhofer (IAO)
GERMANY
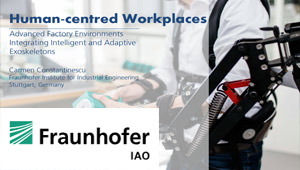
The employment of Exoskeleton in manufacturing represents an innovative technology for handling challenges such as decreasing the employment rate, manual handling of heavy parts and safety and security at workplace. The presentation mainly focuses on modelling methodology for coupling the active and passive Exoskeleton on standard digital humanoid. The current existing methodology could be used for further couplings of the not yet existing Exoskeletons. Before employing an Exoskeleton into the production environment, simulations of “as it is” and of “as it should be” states, need to be performed. The comparison between the simulation results will prove if there exists a real need for the Exoskeleton employment or the workplace should be improved. These simulations reveal the layout constrains, the benefits which the employment of the Exoskeleton brings, and the new ergonomics results for the human workers.
The Challenges of Making a Highly Ergonomic Exoskeleton
Mawashi Science & Technologie
CANADA
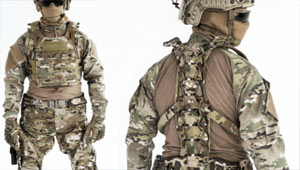
As for cars and phones, exoskeletons will evolve following the advancement other technologies such as robotics, manufacturing processes and materials. Through that evolution the design will be optimized and benefits for the user will be improved. Among all the characteristics to be considered for the development of exoskeletons, ergonomics is crucial to achieve a good human/machine interface. Typically, the design orientation of an exoskeleton can be split into two equally relevant approaches, each having benefits and drawbacks depending on their application. The first one entails a low profile design, close to the body. This approach has the advantages of being potentially low bulk and lightweight. However, it comes with great ergonomics challenges because of the proximity with the body. The second approach involves the use of structures positioned further away from the user’s body. In that case, ergonomics can be achieved at the cost of heavier structures and higher bulkiness. Find more at www.mawashi.net
Exoskeletons: A reasonable supplement to automation
German Bionic
GERMANY
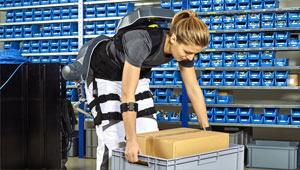
According to the Federal Institute for Occupational Safety and Health (BAuA), musculoskeletal injuries, caused by strain lifting and carrying at work, account for 23 % of sick days in Germany, leading to an estimated annual 10 billion Euro loss in production. Active exoskeletons, like German Bionic´s CRAY X, were created in cooperation with leading work ergonomists specializing in manual hand lifting of goods and tools. Wearing those power suits while lifting heavy loads reduces compression pressure in the lower back area, thereby preventing workplace accidents and musculoskeletal injuries.
Exoskeletal devices in a rehabilitative environment and their challenges in the production of a hybrid intentionality
Universität Konstanz
GERMANY
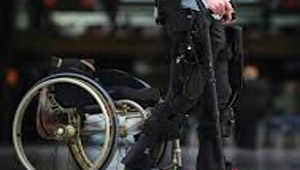
To answer the needs of a motility deficient body may refer both to the scientific conception of a technological object conceived to assist the disabled person, for instance exoskeletal device, and its appropriation by the user. Intentionality is one of the parameters focused by engineers in this process. While using qualitative empirical material (engineers and motility experts discourses and narrative interviews with persons using or having used exoskeletons) and relying on the conceptual background of a recent theoretical paradigm, such as enactive phenomenology, it shall be shown what challenges exist while reconceiving motility intentionality in cases of spinal cord injury and cerebrovascular accidents. In a further step, it shall be focused how these challenges are addressed by designers of exoskeletal devices for this category of subjects. The aim is to confront the user’s subjective point of view with the point of view of specialists working in rehabilitative robotics.
Comau MATE: from workers, for workers
COMAU
ITALY
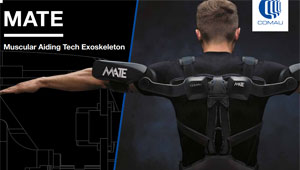
MATE, Comau Exoskeleton, is an ergonomically designed spring-based structure which eases the repetitive movements and relieves the effort, thanks to a lightweight, breathable and effective postural support. Find more at www.comau.com
Empowering human operators in I4.0: challenges, achievements and perspectives based on EURECA and. EFFORTLESS projects
CNR-STIIMA
ITALY
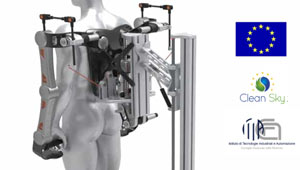
In the context of the factory of the future scenario, a human-centric work-scene is the focus of such industrial revolution, requiring robotics to assist humans, even physically. In order to improve the ergonomics of tasks, together with productivity and flexibility of production, cooperative and wearable robotics is increasingly demanded. The proposed contribution aims at describe challenges, achievements and perspectives of human operators empowering in the context of Industry 4.0. The discussion is based on two on going projects: H2020 CleanSky 2 EURECA (empowering human operators in aerospace industry) and EFFORTLESS (empowering human operators in automotive industry) projects, describing the designed solutions in terms of both hardware and control and discussing about current TRL. A particular focus is made on human-robot interaction, analyzing different metrics for its evaluation, allowing to improve control performance.
Twin: a Lower Limb Exoskeleton for Medical Use
Fondazione Istituto Italiano di Tecnologia
ITALY
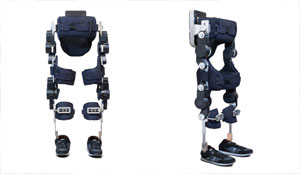
Stroke, together with spinal cord injury (SCI), count up to 52% of the adult-onset disability. Enhancing the process of recovery of cognitive and motor functions after a neurological injury or disease is therefore widely recognized as a priority in healthcare. One of the opportunities in this direction lies in combining traditional approaches with robotic-based neurorehabilitation, thus improving the beneficial effects of the treatment. In this work, we present a novel exoskeleton device and propose its use in neurorehabilitation application scenarios.
Wearable Ergonomics - Using Wearable Sensors to Evaluate Exoskeletons in the Field
Briotix
USA
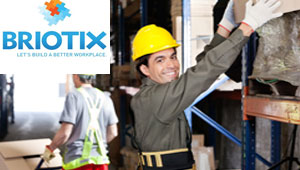
Work related injuries are a major problem in the USA and around the world. Back and shoulder injuries are especially problematic and costly. A number of exoskeletons have been developed to address these problems, but do they actually work, and what are the long term user implications? We have tested a number of exoskeletons with various wearable sensors and a standardized functional movement testing approach and would like to share our results.
Exoskeletons : Past, Present and Future
SkelEx
THE NETHERLANDS
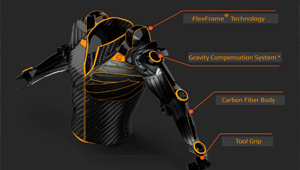
This talk focuses on the future of exoskeletons, from the vantage point of today while keeping in mind learnings from the past. As we live in a time where such devices will become mainstream, we will discuss needs of real users as well as the subjective nature of this challenge. The main issues while using an exoskeletons in a practical setting will also be discussed, followed by the best strategies to tackle them. There will also be a demonstration of the latest SkelEx prototype - a non powered upper body exoskeleton for working in the front or overhead. Members of the audience will have the opportunity to try the device at the end of the talk. This talk will be interesting for those who want to develop themselves in the field of exoskeletons, or for those who are enthusiastic about modern robotics and their applications.
Innovative Methodology for Efficient Control of Human-robot Systems
Bulgarian Academy of Sciences
BULGARIA
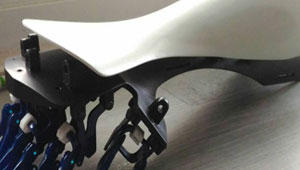
Motor control is complicated for people with robotic devices (prostheses, orthoses, exosuits, and the like). We propose an innovative and generic methodology for efficient control design in various motion/posture tasks, incl. locomotion. As design criteria we take into consideration motion/posture stability, movement execution time, energy expenditure, and the principle of "assistance-as-needed". For posture stabilization we can design robust feedback controllers usng special design relations. We have developed also a control learning approach that optimizes the performance within a minimum number of test movements. The proposed approach has the necessary mathematical and computation guarantees for its feasibility and optimality.